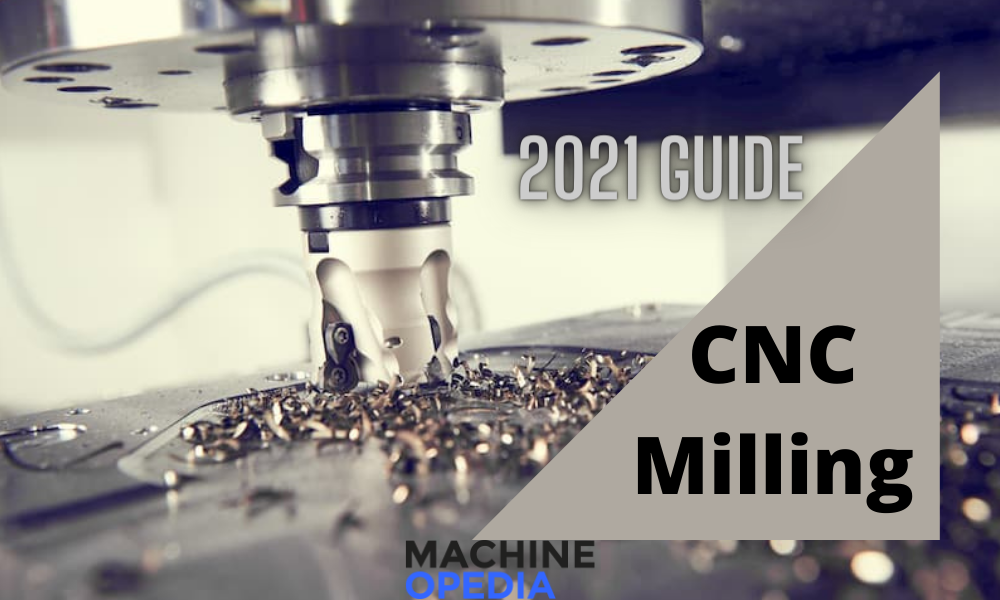
Milling is one of the major types of CNC machining alongside CNC turning in which they can produce a wide range of parts, from basic structures to the most precise ones with the tightest tolerances and complex geometries. And because of this, CNC milling is considered to be one of the most important methods of subtractive metal fabrication.
The demand for rapid prototyping continuously grows as new inventions continue to emerge with the advancements of our technology today, which is why this is one of the major use cases for CNC milling. And due to the availability of a wide range of affordable raw materials (milling plastics and cheap aluminum alloys) and the convenience of CNC milling services, it is one of the quickest and cost-effective ways of producing functional prototypes.
These include replacement parts and even toolings that need to be fabricated immediately. Due to its versatility, CNC milling parts solve the gaps for obsolete and special parts that cannot be bought as standard in the market.
CNC milling has the capability of producing high strength and precise components, and that is why the majority of milling machine parts are used for the production of actual pieces crucial in different applications like the aerospace, automotive, and medical industries
The growing client base of over a thousand satisfied customers is a living testimony of prototype manufacturers’ dedication to providing high-quality products with extended client support, from the customer’s idea to the product design and until the actual production of their milled parts.
The products that companies deliver to their clients are consistently adherent to the customer and regulatory quality requirements.
Generally, some milling services providers are committed to delivering your parts on time as agreed upon.
We have cutting-edge CNC milling machines and inspection equipment that shows your parts are manufactured and inspected with advanced and high-end processes. Through this, we can produce high precision parts that are accurate up to a dimensional tolerance of ± .0005”.
Some prototyping companies have been in the industry for a long time, giving customers
the experience and the expertise of providing clients with solutions to almost any CNC needs.
Through prototype supplier’s advanced processes, they have the flexibility to be ready for any scaling. They will be consistent in delivering high-quality parts from low volume production up to high volume production.
Each profile on a custom part is made through different milling processes; creating a hole is made differently from flattening a surface. Here are the various milling processes you might just need.
This involves cutting the surface of a work part using the radial side of an endmill. The end result creates a flat surface parallel to the radial part of the cutting tool. For producing the best finish for this process, a specialized end mill is used (face mill).
In contrast to face milling, side milling involves passing the side of the cutter (circumferential part of the cylindrical cutter) to the work part vertically in order to produce a flat surface.
This involves cutting the work part so that it forms a slot, an island, a pocket, and many other unique profiles. The cutting tool for this process involves the use of different types of end mills, preferably with side cutting edges.
This includes the creation of general holes, clearance holes (counterbore and countersunk), threaded holes, ports, and many more. Based on the accuracy requirement, there are different cutting tools used, and these are twist drills, porting drills, tap, thread mill, reamers, and many more.
Through these different stages of producing your parts, you can get the manufacturing process as bellows:
Part design: conversion of your part concept and ideas into a workable model.
CNC milling program: setting up machining parameters through a CNC program to successfully cut your parts.
Milling proper: we ensure the right processes are carried on.
Secondary processes: your milled parts can be finished or processed accordingly to your desired output. Depending on your raw material, these can pass through additional processes like superfinishing, surface coating, hardening, anodizing, and painting.
Most of the rapid manufacturing companies can serve many industries from food, heavy equipment, maritime, automotive, medical, and up to the most demanding one, aerospace.
· Aluminum Alloys (6061, 7075)
· Titanium Alloys
· Steel Alloys including different grades of stainless steel
· Inconel
· Acrylonitrile Butadiene Styrene (ABS)
· High-Density Polyethylene (HDPE)
· Polyetheretherketone (PEEK)
· PTFE-Teflon