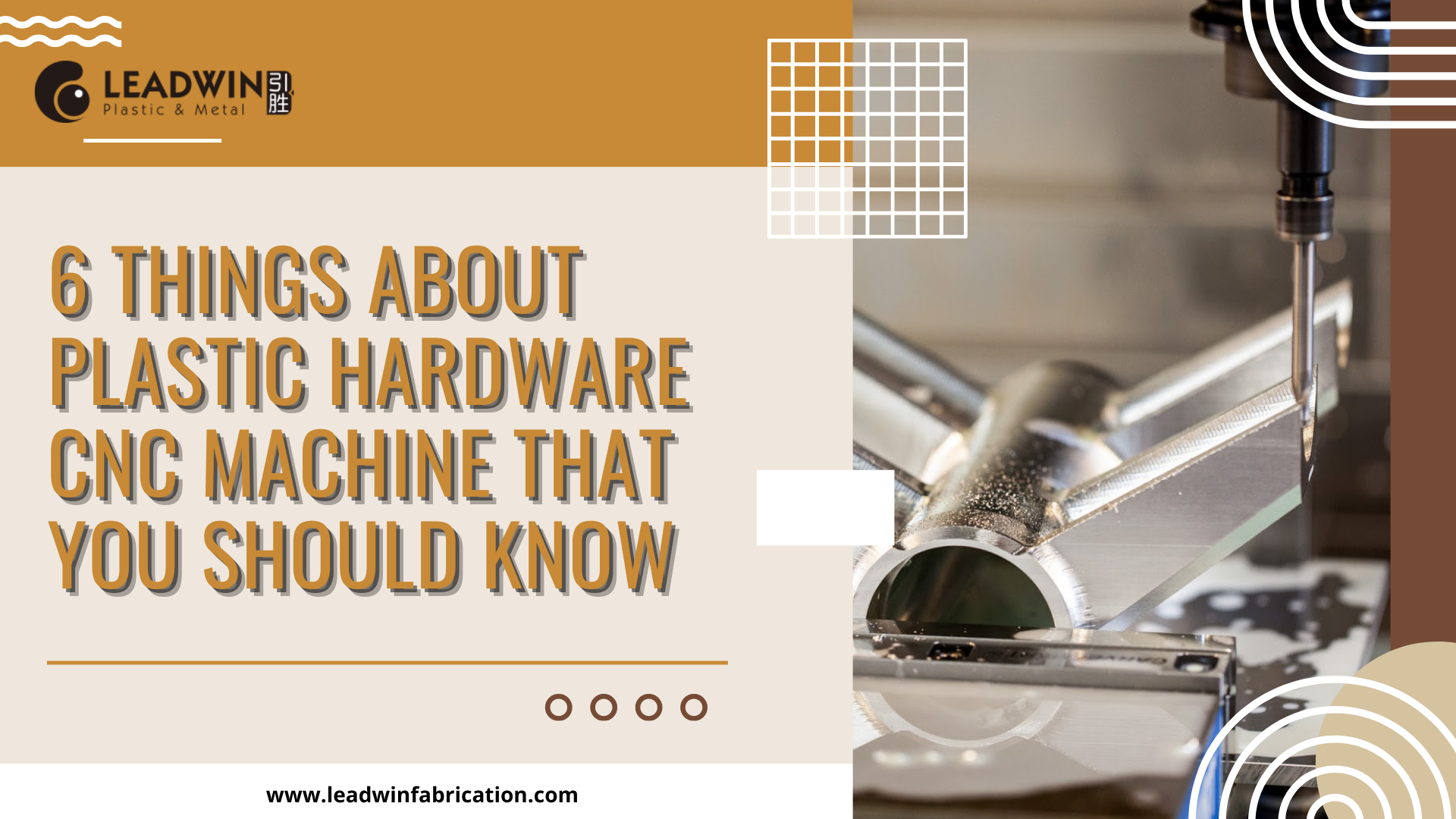
Due to its accuracy, CNC Precision Parts manufacturer, compatibility with complex designs, etc., CNC machining is a standard rapid prototype production process. It is a subtractive process where a computer directs a CNC tool to remove a portion of a workpiece to create the desired result using milling, turning, etc.
Metals, polymers, and wood are just a few of the materials that CNC machines. However, many producers of ABS Plastic components supplier goods now employ plastic CNC machining, which entails producing plastic goods using various CNC machine processes. Plastic CNC machining involves a lot of different things. As a result, this essay will outline seven crucial details concerning the procedure.
Plastic can indeed be CNC-machined. Soft metals are the most typical workpiece material in extensive CNC facilities, according to most people familiar with the procedure. Most fast prototyping service providers will use 3D printing and injection molding to produce Plastic components manufacturer objects.
It does not imply that polymeric polymers cannot be machined. Many CNC machinists enjoy working with plastics because the procedure's benefits complement the material's natural qualities. For instance, cutting polymers is simpler, improving tight tolerance, accuracy, and CNC Precision Parts manufacturer plastics are consequently gaining popularity among companies with higher quality value.
The most popular plastic polymers utilized in CNC plastic machining are thermoplastics. The reform and remodel on melting but keep their original qualities. You can go through our list of CNC materials to have a better idea of and comprehension of what plastic polymer to choose. However, the common plastics listed below can be used for various items.
Thermoplastic Delrin is renowned for its stiffness and strength. As a result of its ability to perform well under conditions of high tensile stress, it makes an excellent plastic for CNC machining.
High purity semi-crystalline nylon is a popular choice for CNC plastic hardware products machining because of its outstanding thermal, mechanical, and chemical resistance. Since nylon has a tight tolerance due to its physical characteristics and dimensional stability, CNC machining is simple. According to the well-known proverb, "machining nylon is like machining brass," it also behaves like a metal. Tungsten carbide alloy tools should be utilized with CNC equipment while working with nylon material.
Lightweight, superior tensile strength, wear resistance, and stiffness make Acrylic a good plastic CNC material. Although there are several conditions you should look for, it has excellent machinability. For instance, to produce a flawless surface finish during CNC cutting, the cutting tool must be made of carbide and have a sharp, aggressive edge.
Teflon, also known as polytetrafluoroethylene (PTFE), is a thermoplastic material that is water-, electrical-, chemical-, and thermal-resistant. Its density and suppleness make it a typical CNC plastic. It is challenging to attain tight tolerances due to its high coefficient of friction and stress creep qualities. Therefore, before Machining, you or the quick prototyping service you choose should be aware of the implications of its qualities and the necessary tools.
A class of high-performance plastics called PEEK, or polyether ether ketone, is renowned for its high melting points, resistance to corrosion, and superior mechanical qualities. PEEK is more frequently used in 3D printing. Still, it is also well suited for Machining because of its inherent qualities and the accuracy, repeatability, tight tolerances, and other benefits of a CNC machine. Even though PEEK is well-known for its use in plastic CNC machining, you should know its qualities to minimize heat and internal stress cracking.
Another CNC plastic machining material with excellent tensile strength, corrosion resistance, and other exceptional mechanical features is ultra-high molecular weight polyethylene. It is a suitable material for quick prototyping due to these characteristics. However, because of its instability, UHMW is difficult to machine. Since the material cannot be molded, Machining is still a preferable choice. As a result, it is preferable to outsource to a company with extensive experience using the material.
Depending on the material and the final result, various methods are involved in plastic machining components wholesale. The three most well-liked processes for plastic Machining out of the several approaches employed in well-known rapid prototyping services are listed below:
In CNC turning, the plastic polymer is turned on a CNC lathe while a fixed CNC tool cuts away a portion of it to produce the desired shape. Even though cylindrical workpieces are the most frequent shape, the method is excellent for various situations. The prototyping service must be aware of several parameters before deciding whether CNC turning is the best method, including the desired product, the outer diameter of the plastic polymer, etc.
In contrast to CNC turning, CNC plastic milling uses stationary material and rotating tools. The tools' corresponding cutting speeds have excellent precision, accuracy, and a consistent output rate, just like CNC turning machine. Additionally, engineered plastic components helpful in working with flat and asymmetrical shapes is CNC milling. During the procedure, a multi-axes, single-point cutting tool is used (the common one is the 3-axis). The versatility of the process and its capability for producing complicated components depend on the number of axes supported.
CNC drilling employs drills as cutting tools to bore a hole through a material. Depending on the type and shape of the drill, pickles of various sections are made in the material. Since CNC machines may also be used for milling and turning, they serve several functions. Additionally, they come in various sizes and call for a professional to guarantee cost-effectiveness while producing plastic components.
In CNC plastic machining, a flawless finish depends on the methods used and a grasp of the material's characteristics. Follow these recommendations to prevent this and get a beautiful finish for your plastic product;
• It should avoid any cutting tool with complicated geometry.
• Don't feed the material faster than what the manufacturer recommends.
• Plastic components that need to be machined need to be securely held in place. Vibration caused by improper clamping of materials will further result in a poor finish on the plastic.
• Additionally, the cutting speed must be within the advised range for various plastics.
Understanding the diverse qualities of plastic materials is necessary to consider these factors. However, by employing finishing methods like annealing, sandblasting, powder coating, etc., you can further enhance the surface finish of any plastic product. You can contact us for advice on selecting the best finishing method for your product.
Plastic polymers are frequently used with other rapid prototyping techniques like injection molding and 3D printing. However, its benefits have recently become more popular with ABS Plastic components supplier machining. The three methods are quick and well-known, and each has advantages. However, many people today favor CNC plastic machining capabilities for the following reasons:
The three quick prototyping techniques all lack the precision and accuracy of CNC plastic machining. The incredible precision and accuracy enable excellent repeatability because the method produces plastic goods of comparable quality across the board.
ABS Plastic component polymers are utilized to create both sophisticated and straightforward goods. Plastic objects with complex designs can be made using CNC plastic machining. Although 3D printing likewise claims a remarkable capacity for intricate constructions, CNC machine tools' precision and accuracy give the method the upper hand.
Of the three techniques, CNC plastic machining is the most effective at producing items with precise tolerances. It is a crucial procedure for most plastics manufacturers because of its accuracy and precision.
All techniques work with a variety of materials. However, CNC plastic machining is trouble-free with a broader array of rigid plastics.
Different plastic polymers have various characteristics, which lead to multiple applications.
• Here are some typical uses for CNC plastic parts:
• Production of implants and medical devices.
• Utilize in the production of plastic components for the food and beverage sectors.
• Manufacturing electrical gadget insulating properties
• Making components for vehicles and aircraft
• The making of lenses (e.g., Acrylic is known for its optical activity)
Numerous commercial and domestic products are made with plastic polymers. A high degree of precision, accuracy, tight tolerance, etc., is required for some items. Therefore, CNC plastic machining has been a top option for many seeking robust and high-quality plastic polymers.