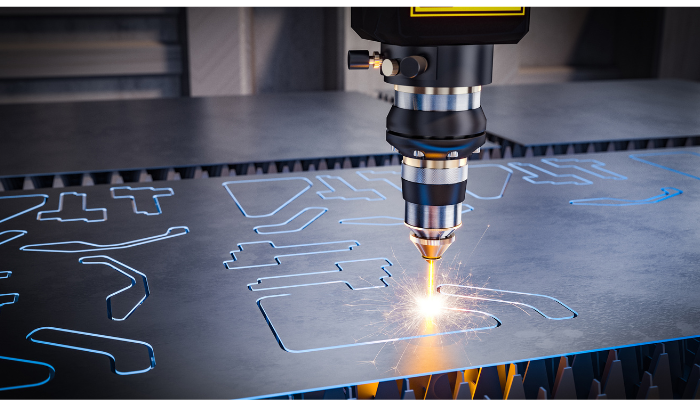
Cast iron is a popular material for manufacturing parts thanks to its excellent strength, durability, and wear resistance properties. However, machining cast iron parts is a bit challenging task, even for seasoned professionals. The material's brittle nature, the tendency to produce dust and chips, and poor thermal conductivity lead to various issues during the machining process, such as poor surface finish, tool wear, and heat-related damage.
Here are some tips for achieving precision CNC machining and surface finishing of cast iron parts.
Choosing the right tooling and selecting the correct cutting parameters is o essential, but the selection of the proper cutting tool and machining parameters is critical when working with cast iron. Carbide tooling or ceramic inserts are the most suitable options for machining cast iron parts, as it has the ability to withstand the high cutting forces and high temperatures produced during the process. High-speed steel (HSS) tools are not recommended for machining cast iron because they tend to dull quickly and produce excessive heat, which leads to thermal damage to the workpiece. Using low cutting speeds and high feed rates help prevent the buildup of heat and reduces tool wear. Optimizing the tool's rake angle help reduce the cutting forces and improve the surface finish.
When machining cast iron, the use of an appropriate coolant and lubrication plays a pivotal role. Coolants help reduce heat buildup and flush away chips, while lubricants reduce friction and prevent tool wear, but be aware applying too much coolant can cause thermal shock and lead to cracking or warping of the workpiece. However, it's crucial to use a coolant and lubricant that is compatible with cast iron, as some types can cause surface staining or corrosion. Water-soluble coolants are mostly the best for cast iron machining, as they provide excellent cooling and lubricating properties while being easy to clean. However, they should be formulated to minimize the risk of staining and corrosion. Mineral oil-based lubricants are also used to reduce friction and wear. It is recommended to use a minimum quantity lubrication (MQL) system that delivers a small amount of coolant directly to the cutting zone.
Cast iron's abrasive nature wearing of tools, and poor surface finish caused problems that are faced by the professionals and compelled them to take measures to minimize these issues. Using sharp tools, optimizing the tool's geometry and coating, and controlling the machining parameters help reduce tool wear and improve surface finish. Using multi-edge cutting tools can help reduce tool wear and prolong the tool's lifespan. Use a specialized cutting tool that is designed for finishing cast iron parts. These tools have a specific geometry and coating that helps to reduce chatter and improve surface finish.
One of the most significant challenges of machining cast iron is managing the chips and dust generated during the process. Cast iron is brittle and can produce sharp, jagged chips that can cause damage to the workpiece, the tool, or the operator. In addition, the dust produced during the machining process can be hazardous to health and safety.
To manage the chips and dust, it's crucial to use an appropriate chip and dust management system. A well-designed chip and dust management system can help reduce the risk of damage, improve surface finish, and maintain a safe and clean work environment. Chip breakers, chip deflectors, and chip conveyors are all effective ways of managing chips, while dust collectors and air filtration systems can help reduce the amount of dust in the air.
Cast iron parts can be heavy and challenging to hold securely, making it essential to use the right fixturing and work-holding solutions to ensure the workpiece remains stable and accurate during the machining process. There are several work-holding solutions available for machining cast iron, such as vise jaws, magnetic chucks, and clamps. The choice of work-holding solution will depend on the size, shape, and complexity of the workpiece. For example, magnetic chucks are suitable for flat or cylindrical parts, while vise jaws are more versatile and can accommodate a range of shapes and sizes.
it's important to ensure the workpiece is positioned correctly relative to the tool. This can be achieved by using dial indicators, edge finders, or other positioning tools.
The type of machining center used can also affect the precision and quality of cast iron parts. Vertical machining centers (VMCs) are commonly used for 3-axis milling and drilling operations, while horizontal machining centers (HMCs) are better suited for 4-axis and 5-axis machining, as well as high-volume production. HMCs can provide better access to the workpiece and reduce tool change times, while VMCs can offer a more compact footprint and easier programming. Choosing the right machining center depends on the specific requirements of the project, such as the complexity of the part geometry, the size of the workpiece, and the desired production volume.
Pre-machining preparation also affects the outcome of CNC machining of cast iron parts. For instance, the workpiece should be properly fixtured to ensure stability and accuracy during machining. The cutting tools should be properly placed and tightened to prevent tool runout or chatter. The workpiece should be properly cleaned and inspected for any defects or impurities. By paying attention to these details, manufacturers can avoid common issues such as tool breakage, surface damage, or dimensional errors.
Adaptive machining technologies such as real-time tool wear monitoring, machine learning algorithms, and closed-loop feedback systems play their role in improving the precision and efficiency of CNC machining cast iron parts especially in CNC machining auto parts. Real-time tool wears monitoring help detect and predict tool wear based on cutting force, temperature, and other parameters, allowing operators to adjust cutting conditions or replace tools as needed. Machine learning algorithms analyze data from multiple sources to optimize cutting parameters and reduce cycle times. Closed-loop feedback systems can adjust the cutting conditions based on the actual measurements of the workpiece, ensuring consistent quality and accuracy.
Cast iron is a broad category of materials that includes various types, such as gray iron, ductile iron, malleable iron, and white iron. Each type of cast iron has different properties that affect the machining process, such as hardness, strength, ductility, and abrasiveness. Therefore, it is important to optimize the cutting parameters for each type of cast iron to achieve the best results. For instance, gray iron is generally easier to machine than ductile iron, but it may require higher cutting speeds to prevent work hardening. Ductile iron may require lower cutting speeds but higher feed rates to avoid chipping.
Finally, collaborating with experts in cast iron machining can provide valuable insights and resources for manufacturers who want to optimize their CNC machining process. Experts can provide technical assistance, training, and support for tool selection, cutting parameters, surface finishing, and post-processing. They can also recommend best practices, quality standards, and industry trends. By partnering with experts in cast iron machining, manufacturers can improve their competitiveness, efficiency, and profitability in the global marketplace.
Surface finishing is an important step in machining cast iron parts, as it can affect the final product's appearance, corrosion resistance, and fatigue strength. Some common surface finishing techniques for cast iron include grinding, honing, and lapping. Grinding is a popular choice for achieving a smooth surface finish, but it can also generate a lot of heat and cause residual stress in the workpiece. Honing is a gentler method that can produce a crosshatched surface pattern and improve lubrication retention. Lapping is a precision technique that uses abrasive compounds to remove small amounts of material and achieve a high degree of flatness and parallelism.
After machining and surface finishing, it is important to perform some post-processing steps to ensure the quality and integrity of the cast iron parts. These steps may include inspection, cleaning, deburring, and coating. Inspection can help to detect any defects or deviations from the design specifications, while cleaning and deburring can remove any residual debris or sharp edges that may affect the performance or safety of the parts. The coating can provide additional protection against corrosion, wear, and friction.
Surface finishing is an important step in machining cast iron parts, as it can affect the appearance, corrosion resistance, and fatigue strength of the final product. Some common surface finishing techniques for cast iron include grinding, honing, and lapping. Grinding is a popular choice for achieving a smooth surface finish, but it can also generate a lot of heat and cause residual stress in the workpiece. Honing is a gentler method that can produce a crosshatched surface pattern and improve lubrication retention. Lapping is a precision technique that uses abrasive compounds to remove small amounts of material and achieve a high degree of flatness and parallelism.